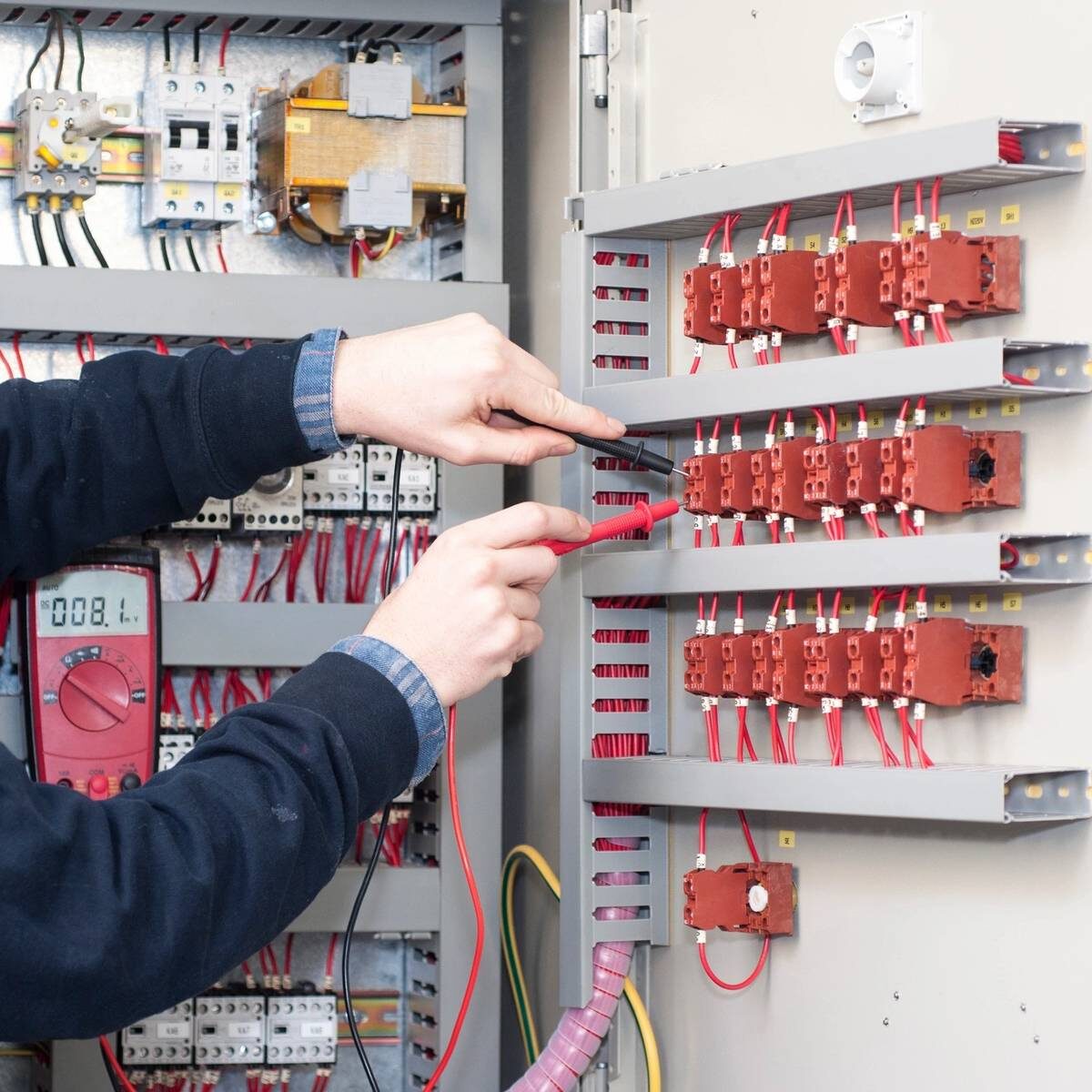
One-of Solutions
EVIDENCE THAT A SOLUTION IS NEEDED
If you are saying to yourself “There must be a better way to do this”, then lets start a conversation! Opportunities for improvement are usually found when you notice any of the following:
- Repetitive work: If 100 employees perform a task 10 times per day across 200 workdays per year, shaving just 18 seconds off each task can save the company 1,000 hours annually.
- Waste of any kind: Tasks where the setup effort exceeds the actual tangible output. Designs that needlessly waste material. Field fitting material that could have been manufactured better. Process that breaks down the minute a certain person leaves on vacation
- SCALIBILITY ISSUES: Where growth in output of a process is proportional to labor hours at a 1:1 ratio.
- employee frustration: Good employees voice frustration. When good employees have problem solving ideas, but face obstacles to producing high-quality work they are proud of.
- Poor quality or complicated end productS: Maybe the wrong tools were used for the job? This leads to a needlessly complex or poor-quality end product.
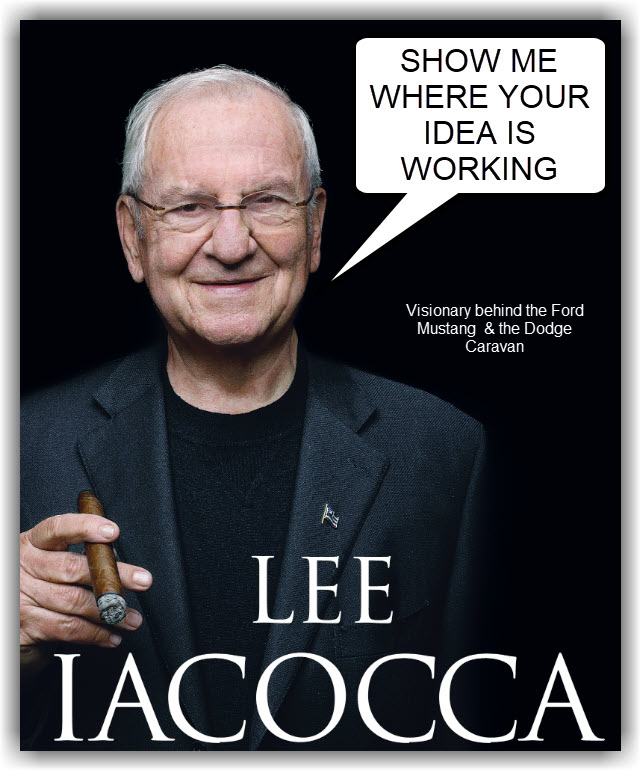
SAMPLE SOLUTIONS
No two problems are identical, and neither are the solutions. The solution to your problem will be unique, but maybe some successful ideas will prime the imagination:
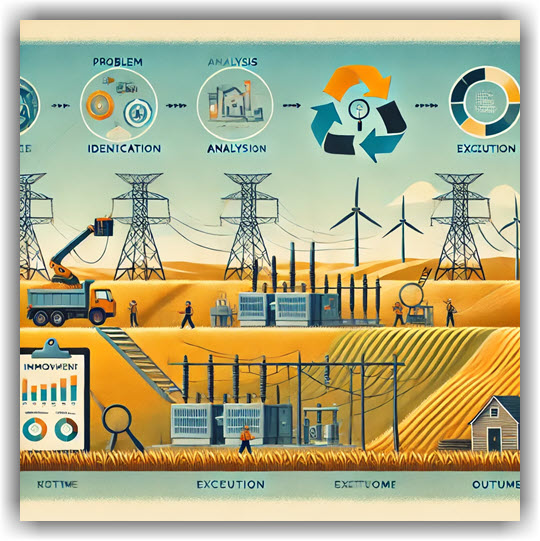
- Custom Physical Tool Design: From portable shelters that can be set up in under 5 minutes for winter work on AMI cabinets to a DIN rail sheer. We can bring ideas to life in partnership with fabrication experts.
- Custom Digital Tool Design: Often, the data and functionality we need are already available in existing tools; we just need to find the right way to use them. For example, using PowerBI data plugged into GIS to map powerlines obstructing high-load moves, or leveraging SAP for forecasting material usage by estimating based on template designs. And, of course, if all else fails, every Excel power user loves crafting a custom spreadsheet.
- Minimum Viable Product (MVP) Development: My then-manager, an innovation leader, asked, “Before we commit extensive time, what will it take to demonstrate that using video for scalable training works?” I responded with “One site visit and 8 hours.” The rest is history!
- Business Process Improvement: Mapping out the interdependencies of the wood pole replacement program in swim lanes revealed that a single pole with environmental concerns could stall the entire batch. We responded by moving environmental screening to before engineering and handling poles with concerns as separate orders.
- finding best practices – don’t reinvent the wheel: Instead of reinventing the wheel, we asked, “What are other utilities doing that works?” As part of the OH&S committee, we needed guidance on handling worker injuries on top of transformers. A coworker connected us with a friend from another utility who shared their documentation. We were able to test their methods, confirm they met our needs, and rapidly implement the changes.